在注塑成型过程中,毛边(飞边、批锋)是最常见的缺陷之一。它不仅影响产品外观,还可能导致模具损坏、生产效率下降,甚至引发安全隐患。
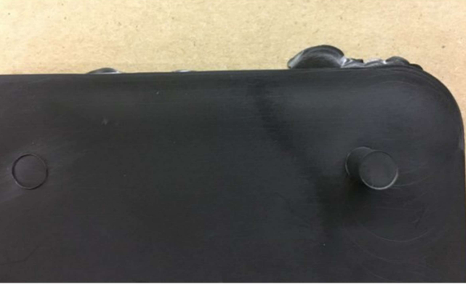
图1 毛边
本文将从毛边形成原理出发,深入分析注塑工艺、模具、设备和材料四大核心环节的潜在问题,并提供实际案例和解决方案毛边困扰!
一、毛边是如何产生的?三个关键条件必须满足
毛边是塑料熔体从模具分型线或配合面溢出的结果。要避免毛边,必须满足以下三个条件:
1️⃣ 锁模力 > 型腔压力:注塑机锁模力需足以抵抗塑料填充时的型腔压力。
2️⃣ 模具结构稳固:模具在锁模力和型腔压力下不发生变形。
图2 力的作用方向既平行又垂直于锁模力
3️⃣ 分型线完美贴合:分型面无缝隙、无损伤,所有封胶面紧密闭合。
二、四大核心原因及解决方案
01 注塑工艺问题:参数不当是“元凶”
-
① 二段压力过高
原因:过高的保压压力会撑开模具分型线。
解决:降低二段压力,优先优化模具收缩率设计,避免依赖高压补缩。
-
② 填充过量(仅填充重量过大)
案例:某平板制品因填充切换点过晚(>98%),导致型腔压力骤升,分型线溢料。
解决:通过短射测试校准填充切换点(95%-98%),并检查模具是否匹配工艺。
图3 切换过晚产生毛边的制品 -
③ 锁模力不足
检测方法:用百分表或过程监控系统观察模具分型线位移。
解决:校准注塑机锁模力设置,检查肘杆磨损或液压阀泄漏问题。
图4 注塑型腔投影面积 -
④ 熔体温度异常
高温问题:材料黏度降低,易渗透分型线缝隙。
低温问题:填充阻力增大,被迫提高压力导致锁模失效。
关键参数:料筒温度、背压、螺杆转速需与材料特性匹配。
-
⑤ 速度-压力转换不当
案例:矿物填充PP制品因V-P切换时压力突增产生毛边。
解决:优化保压体积百分比,采用平滑压力控制曲线(如RIGeDART技术)。
图5 不良的速度-压力响应:注意压力先下降后上升
02 模具问题:结构缺陷是“硬伤”
-
① 分型线损坏
原因:钢材磨损、抛光过度、碎屑卡入。
修复:激光焊接后精细抛光,避免二次损伤。
图6 分型线错边 -
② 排气槽过深
关键:尼龙等低黏度材料需严格控制排气深度(通常0.01-0.03mm)。
技巧:增加排气宽度而非深度,降低溢料风险。
图7 PA66材料排气槽设计案例 -
③ 滑块/型芯支撑不足
计算法则:液压缸推力需 > 型芯面积 × 型腔压力(图)。
设计优化:斜楔块预紧结构可增强滑块抗压能力。
图8 计算所需油缸尺寸 -
④ 模具变形
高风险区:顶针板、热流道分流板区域支撑柱缺失。
预防:定期检查支撑柱压痕,避免模板下沉变形。
图9 显示模具变形的过程监控曲线
03 注塑机问题:设备状态不容忽视
-
① 锁模力不均
检测:通过拉杆拉伸量测试锁模平行度(误差需<0.003英寸)。
维护:定期清洁模板表面,校准模具高度。
-
② 肘杆磨损
征兆:锁模动作迟缓、异响。
后果:局部锁模力下降,分型线单侧溢料。
-
③ 模具尺寸不匹配
禁忌:小模具装大机器易导致模板翘曲,中心区域锁模力不足。
对策:使用支腿支撑柱分散压力。
04 材料问题:特性变化引发连锁反应
-
① 黏度降低
诱因:材料水解、回料过量、添加剂比例异常。
检测:熔体流动速率(MFI)测试,对比批次差异。
-
② 含水率超标
现象:熔体稀软、气泡多,清理时无法成条。
解决:严格执行材料预干燥工艺(如尼龙需120℃烘干4小时)。
-
③ 回料使用不当
原则:回料需清洁、无降解,立即粉碎回用。
禁忌:银纹、烧焦等缺陷料禁止重复使用!
三、实战案例:锁模力泄漏引发的批量毛边
背景:某汽车部件生产时,分型线单侧频繁溢料,调整工艺无效。
排查:旋转模具180°后,毛边位置不变,锁定注塑机问题。
根因:锁模油路阀泄漏,实际锁模力仅为额定值的70%。
解决:更换液压阀后,锁模力恢复,毛边消失。
四、总结:系统思维是关键!
毛边问题往往由多因素叠加导致,需采用STOP分析法(Suspend暂停→Think思考→Observe观察→Plan计划)逐步排查:
-
优先检查工艺参数:锁模力、熔温、V-P切换点。
-
模具状态排查:分型线损伤、排气槽深度、滑块支撑。
-
设备维护:拉杆平行度、肘杆磨损、锁模力校准。
-
材料管理:批次一致性、含水率、回料管控。
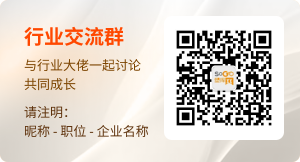