工业 3D 打印公司 Essentium 对 Collider 及其 Orchid 打印机技术的收购,以及北佛罗里达大学 (UNF) 教授 Steve Stagon 的 3D 打印模具专利提高了在寻求减少或消除成本高昂的工具的同时优化生产的标准执行更大批量的零件。
在获得 Collider 的技术后,Essentium 坚定地致力于通过数字光处理 (DLP) 实现可编程工具,该技术可在同一个构建室中打印出可溶解的薄光聚合物外壳并填充传统的热固性聚合物。
“我们相信可编程工具和我们 Orchid 平台的其他部件将有助于推动基于聚合物的 Additive 2.0 的革命,”位于德克萨斯州 Pflugerville 的 Essentium 光聚合物总监 Graham Bredemeyer 说。该技术生产“模仿注塑成型
和数控加工等传统技术的强度和表面质量的零件——但时间很短。”
技术加快了开发和生产的时间表
就生产目标而言,Essentium 更愿意“考虑每天生产 50 到 1,000 个或更多零件所需的机器组的活动,”Bredemeyer 补充道。“我们认为这将我们客户的开发和批量生产时间缩短数月甚至数年,尤其是在医疗、军事和运输领域。”
3D 打印使复杂几何形状的设计和生产成为可能。
Bredemeyer 解释说,这种两全其美的方法利用了 3D 打印和成型的核心优势。
“DLP 直接打印工艺生产的零件与所使用的树脂一样好。如今,光敏树脂不如用于注塑成型或 CNC 加工零件的现成材料坚固。Collider 技术使用更广泛的热固性聚合物作为成品部件的基础,因此不会受到这些限制。”
工艺克服了 3D 打印塑料模具的挑战
同时,Stagon 的具有优化涂层和冷却通道的印刷注塑模具的专利瞄准了一个想法,“相当多的团队已经研究过”,他说 - 生产性能尽可能与金属模具匹配的聚合物模具,以节省时间和钱。
杰克逊维尔教授说,Stagon 的模具针对中小批量,以及几何形状略有不同的零件系列。“在这个领域,传统模具不具有成本效益——小批量的资本投资太多。” 但是打印聚合物模具的尝试遇到了几个问题:
-
模具热撕裂并迅速失去边缘和表面特征。“您只能在每个模具上取出少量零件,在更换工具和准备新的印刷工具时会消耗利润,”Stagon 解释说。 -
冷却不良意味着循环时间要长 10 到 100 倍,凝固和均匀性可能成为问题。“由于传热差异,全聚合物印刷模具的表现非常不同,我们的合作伙伴在流程上花费了太多时间来调整——再次削减利润。”
UNF教授的解决方案?创建一个过程,保留表面特征“超过少数零件并提高热导率接近一个点,从而减少调整注射参数。在高运行生产中,金属模具仍然是,并将永远是,王者。我们的工作使小批量更接近铝模具,并使工作流程更快,调整更少。”
对于模具的涂层,Stagon 借鉴了传统模具的技术。
“我们将化学镀和气相沉积或‘溅射’结合起来,首先‘撞击’模具表面,使其具有导电性。然后我们镀上 1 到 50 微米的 eNi、NiP 或 CoP。这为我们提供了一个非常坚固的层,可以很好地导热。在此之上,我们采用了经典的模具涂层,如 PTFE Ni 和化学镀镍硼。通过使表面光滑并具有良好的润滑性和释放性,我们能够更长时间地保留厚结构涂层,并减轻聚合物和镀层之间的附着力。”
同时,3D 打印让 Stagon 将冷却通道靠近特征并将它们相对于内部模具特征定位。“凭借表面金属涂层的强度,在某些情况下,当注射压力保持较低时,我们能够将厚度减少到一厘米或更小。我们正在努力为此获得良好的温度曲线数据,但在早期原型中,我们发现冷却时间减少了两倍。”
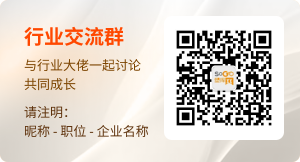