注塑成型过程中,烧焦是常见的缺陷之一,严重影响产品外观和质量。本文将深入分析烧焦问题的成因,并提供系统的解决方案。
一、什么是烧焦缺陷?
在注塑填充过程中,若气体被困于模具型腔,高压下可能引发燃烧,导致制品表面出现黑色烟尘状沉积物(如图)。这种缺陷俗称"困气""烧黑"“burning”,易与混色、黄纹、黑纹混淆,但本质是气体燃烧残留物。
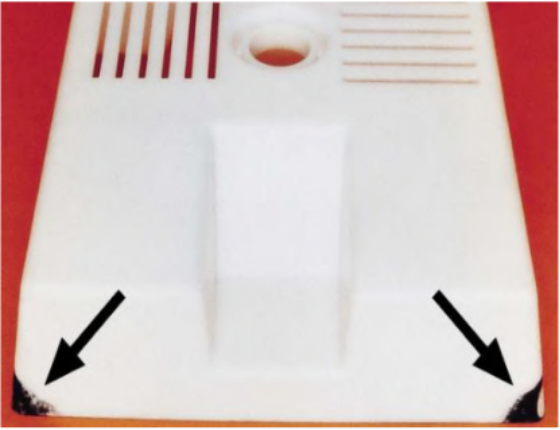
图1 烧焦
二、烧焦根源:气体从何而来?为何排不出?
01气体来源
-
模具型腔原有空气
-
材料高温分解(含水量高、添加剂挥发)
-
螺杆/料筒积垢产生的挥发性气体
02
排气失效关键原因
✅ 模具排气不足(占90%以上案例)
✅ 填充速度过快 → 气体被高速熔体"封死"
✅ 熔体温度过高 → 材料分解产气
三、系统排查与解决方案
01 注塑工艺因素
1.1 填充速度过快
填充速度过快时,气体更易被困在模具内而非通过排气孔排出。
解决方法:
-
降低填充速度(临时方案)
-
从根本上解决:改善模具排气
案例:某产品在填充末端熔接线处出现烧焦,降低填充速度后问题解决。随后加深排气孔,使填充速度恢复原值,不仅实现更快填充,还节省了2秒以上的成型周期。
1.2 熔体温度过高
高温加工可能导致材料降解,产生气体副产物。
解决方法:
-
检查实际熔体温度(建议用接触式测温仪测量)
-
确保料筒温度设置正确
-
检查背压和螺杆转速(螺杆应在冷却结束前2-3秒完成后退)
图2 用测温仪实测熔体温度
1.3 松退设置不当
过度松退会导致空气在喷嘴尖端被吸入熔体。
解决方法:
-
检查并调整松退量
-
如为控制喷嘴流涎而设置大松退量,应先检查喷嘴温度
02 模具因素
2.1 排气不足
模具排气不足是导致烧焦的首要原因!
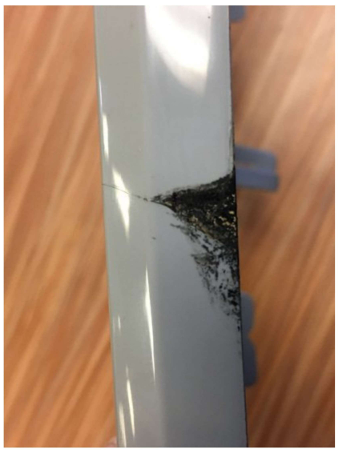
图3 熔接线处排气不足导致烧焦的典型案例
解决方法:
-
清洁模具排气孔(包括滑块和斜顶处)
-
增加额外排气
-
定期维护,防止钢材腐蚀
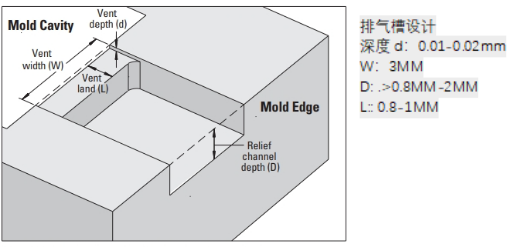
典型的PA材料排气槽设计指引
2.2 模具污染
油脂、油污等污染物可能堵塞排气孔。
解决方法:
-
找出并消除污染源(如液压泄漏)
-
规范模具润滑程序
-
避免将液压连接设置在模具顶部
03 注塑机因素
3.1 积垢问题
螺杆、端盖、止回阀处积垢会导致材料降解。
解决方法:
-
建立正确的关机和清洗程序
-
检查喷嘴与端盖/尖端的匹配度
-
长时间停机前彻底清洗料筒
3.2 螺杆设计错误
不当的螺杆设计会产生过多剪切力,导致材料降解。
图4 典型的通用型螺杆
解决方法:
-
确保螺杆长径比和压缩比适合材料
-
检查螺杆是否有积垢形成的"屏障螺纹"
3.3 料筒加热器温度失控
过热区域会导致材料局部降解。
图5 检测喷嘴热点的红外照片
解决方法:
-
检查料筒温度读数
-
降低螺杆转速或背压
-
检查热电偶安装是否正确
3.4 部件损坏
损坏的部件会产生高剪切区域或积垢。
解决方法:
-
检查并更换损坏的螺杆、料筒、止回阀等部件
-
清除进料系统中的金属异物
04 材料因素
4.1 含水量过高
吸湿性材料含水量高时,水分汽化会导致熔体混入气体。
解决方法:
-
确保材料充分干燥
-
检查干燥设备运行状况
4.2 材料类型
PVC、聚甲醛等温度敏感材料更易烧焦。
案例:某PVC材料试模时出现碳化痕迹,后发现是配方热稳定性不足。
解决方法:
-
严格控制料筒温度
-
关注材料在料筒内的停留时间
-
确保无材料滞留区域
4.3 添加剂问题
色母粒和其他添加剂可能影响烧焦可能性。
解决方法:
-
使用正确的添加剂稀释比例
-
确保添加剂适用于注塑材料
-
深色制品要特别注意检查肋尖等隐蔽部位
四、总结与建议
烧焦问题的解决应遵循以下步骤:
-
优先检查模具排气:这是最常见的原因
-
排查材料因素:特别是含水量和材料类型
-
检查注塑机状态:积垢、部件损坏等问题
-
最后调整工艺参数:如填充速度、熔体温度等
重要原则:不要试图通过调整工艺来掩盖模具或设备问题,应从根本上解决问题!
通过系统排查和针对性解决,可以有效消除注塑过程中的烧焦缺陷,提高产品质量和生产效率。
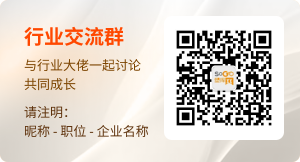