轻量化被视为最直接有效的节能减排措施。排放污染较为严重的汽车行业,轻量化是整个行业亟待解决的关键问题,而碳纤维复合材料的特性恰好契合轻量化对于构件材料性能的苛刻要求,因此其在汽车零部件上的应用得到了广泛研究。
Fibersim拥有独特的复合材料铺覆仿真技术,可帮助工程师在产品设计初期就发现纤维铺覆情况,进而调整产品结构和铺覆方案,保证产品的制造可行性,实现复合材料产品设计、制造及工艺一体化。
上海工程技术大学通过对钢制油底壳进行等刚度替换来初步确定碳纤维制油底壳的厚度,再基于Fibersim软件对构件进行铺覆性分析验证;分别利用分块和剪口处理两种方案对不满足铺覆性要求的铺层进行处理,并分析对比两种方案的优缺点,最后得到具备可制造性的碳纤维复合材料油底壳铺覆方案。
1、碳纤维复合材料油底壳的等代设计
碳纤维复合材料油底壳的等代设计是通过原钢制冲压油底壳的结构进行材料替换设计,由于碳纤维复合材料性能与工艺差异,需对原钢制油底壳的结构进行更改,再进行铺覆仿真分析,确定碳纤维复合材料油底壳的结构形状。
1.1 等刚度替换原理
采用轻量化潜能高的轻质高强材料替换原材料是目前最有效的轻量化方法,在进行材料替换时,通常采用的是等刚度替换原理来初步确定替换后结构件厚度。
通过对公式进行替换转化后可得碳纤维复合材料替换金属材料前后厚度比值:
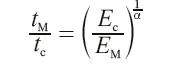
其中,tc、tM分别为替换后碳纤维复合材料结构截面厚度和原金属结构截面厚度,对于汽车零件,α取值通常在1~3之间。
拟采用T700型号碳纤维复合材料单向带配合BAC172环氧树脂,该组合制成的碳纤维复合材料制品力学性能优异且工艺可操作性强。油底壳材料替换厚度指数系数取2.07,基于上述理论公式可得碳纤维复合材料油底壳的初步厚度如下表。
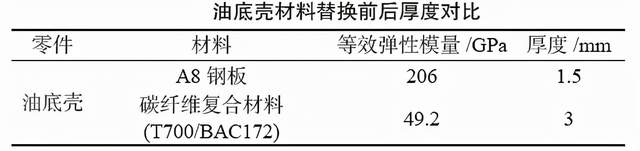
1.2 原金属油底壳结构形式
图1为钢制油底壳三视图与轴测视图。发动机油底壳的主要功能是储存并收集发动机各部件表面的机油,是发动机润滑系统中至关重要的一部分。如图2所示,油底壳多为阶梯状,在四周墙壁上多布有加强筋结构,上表面均匀分布了涂胶槽,通过密封胶与螺栓配合与发动机连接,实现密封,通常在底部还布置有放油螺塞。由于油底壳布置于发动机底部,服役环境恶劣,除满足基本的储油功能外,还要求油底壳要抵抗冷热变化冲击以及承受复杂道路状况的严峻考验。
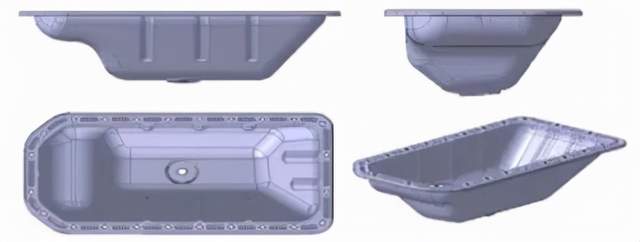
图1 钢制油底壳三视图与轴测视图
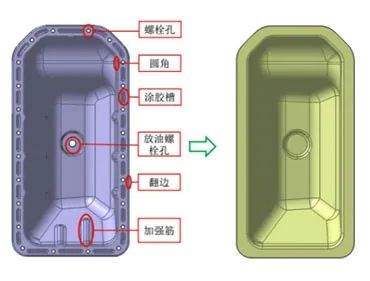
图2 碳纤维复合材料油底壳替换模型
1.3 碳纤维复合材料汽车油底壳的设计
进行钢制油底壳的碳纤维复合材料替换设计,首先需要保证碳纤维复合材料油底壳满足金属复合材料油底壳的功能要求,包括与发动机的密封要求,与放油螺栓的连接要求,满足各工况要求下的强度要求等;然后再保证碳纤维复合材料油底壳的工艺可制造性,最终实现轻量化设计。
如图3所示,原金属油底壳的放油螺栓是通过焊接在油底壳上的螺母进行连接,而碳纤维复合材料无法进行焊接操作,如果考虑在碳纤维复合材料油底壳成型后,将螺母通过胶接粘在油底壳放油螺栓开孔处,在多次拧紧操作下,胶接强度能否满足存疑,因此考虑采用预埋件,如图4所示,在放油螺栓位置处,将金属预埋件埋在铺层中间并定位,与碳纤维复合材料油底壳一起共固化成型,然后在定位的预埋件位置进行攻丝操作,既满足了强度要求又复合了密封要求。
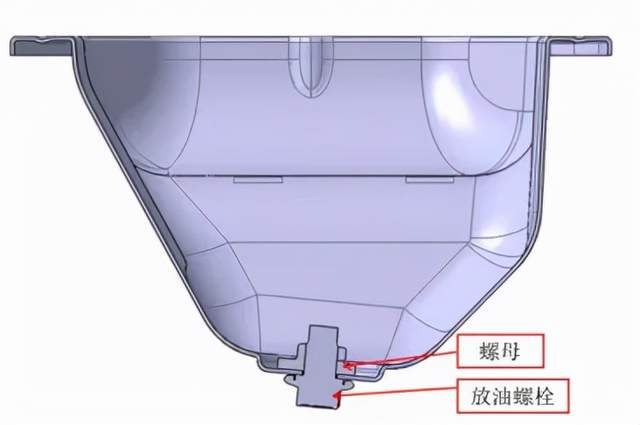
图3 金属油底壳与放油螺栓连接方式截面图

图4 碳纤维油底壳金属预埋件位置截面图
基于等刚度替换原理,初步确定了碳纤维复合材料油底壳的厚度为3mm,每层碳纤维材料的厚度为0.15mm,考虑到铺层结构的连续性,碳纤维复合材料同一角度的铺层为一个整体,因此初步设定碳纤维复合材料的铺层设计为[455/-455/05/905],如图5所示。
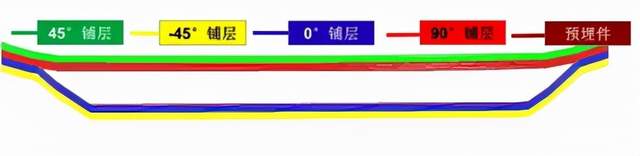
图5 碳纤维油底壳金属预埋件位置处铺层信息图
2 碳纤维复合材料油底壳的铺层工艺仿真
利用集成于Catia的Fibersim软件进行碳纤维复合材料油底壳铺覆仿真,在此之前,需要确定铺覆仿真的五要素,如图6所示。制造边界为实际铺覆时,应当铺覆至最大边界,保证产品留有余量进行修剪加工;设计边界为所设计零件的边界,也即最终成品的边界;铺覆原点一般取铺覆面的中间点,当没有另外确定铺覆点时,默认铺层是从铺覆原点开始向四周铺覆;坐标系0°方向即碳纤维复合材料的纤维方向;铺覆面为铺层铺覆的表面,它决定着铺覆形状和方向。
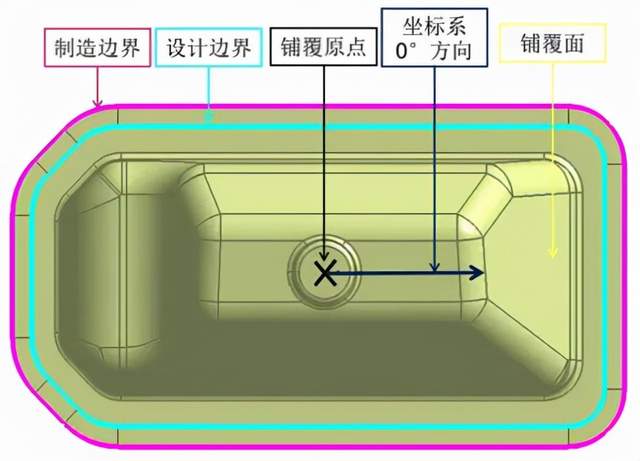
图6 铺覆仿真五要素图
2.1 0°铺层的铺覆可行性分析
从图7a可以看出,在油底壳的四角处出现大片的红色区域,在Fibersim软件中有如下规定,当铺层变形角度大于等于15°,即该区域实际无法铺覆,用红色表示;当铺层变形角度小于15°大于等于10°,铺覆效果一般,可以接受,用黄色表示;当铺层变形角度小于10°,不存在制造问题的区域用蓝色表示。很明显看出在曲率变化范围较大的四角圆角处,产生了实际无法铺覆的结果,通常情况下需要对该缺陷区域进行剪口或分块处理。剪口处理一般在曲率变化大的圆角处进行裁剪,因为曲率变化大,平整的碳纤维布会在圆角处出现褶皱,影响零件的力学性能,如图7b所示,对曲率变化大的6处圆角处进行了剪口处理,0°铺层的铺覆效果大幅提升,原先红色无法铺覆的区域基本变为黄色可接受的区域,只存在些许的红色缺陷区域,该区域可经过后续的真空带压缩使其完成铺覆;分块处理一般沿平行于铺层角度方向进行分块,不伤害沿纤维方向的力学性能,为保证分块少,保证铺层的完整性,并保证铺覆效果,对0°铺层分块如图7c所示,将0°铺层分为竖直三块,且铺覆效果可以接受。
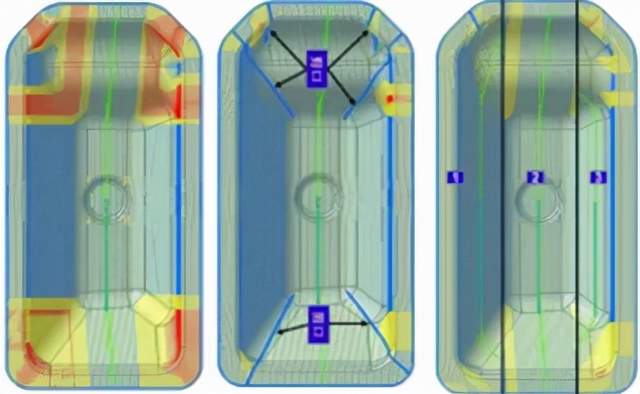
(a) 未处理 (b) 剪口处理后 (c) 分块处理后
图7 0°铺层铺覆效果
2.2 90°铺层的铺覆可行性分析
90°铺层的铺覆缺陷与0°方向的铺覆缺陷相似,采用两种方案处理。在曲率变化大的圆角处进行剪口处理,需要注意的是,剪口位置应与0°方向错开,避免相同位置处出现强度薄弱区域,如图8b所示通过6处剪口处理后,90°铺层的铺层效果可接受。
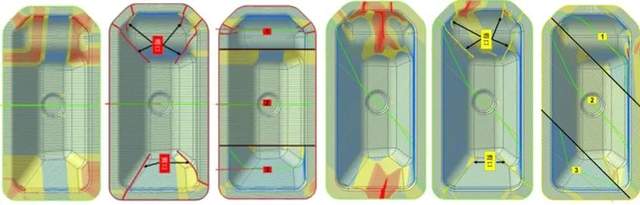
(a) 未处理 (b) 剪口处理后 (c) 分块处理后
图8 90°铺层铺覆效果
2.3 45°铺层的铺覆可行性分析
图9a所示,油底壳不仅出现了红色的铺覆缺陷区域,而且在油底壳右下角和左上角出现了缺料现象,这是因为铺层发生皱褶现象,无法铺平展开。首先采用剪口方案,如图9b所示,通过6处剪口操作,45°铺层的铺覆效果达到了可接受的程度。
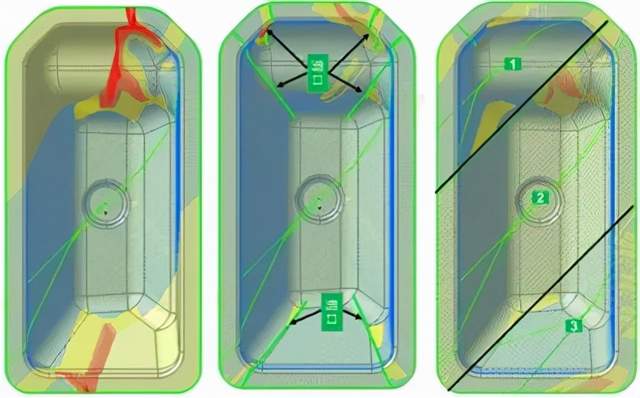
(a) 未处理 (b) 剪口处理后 (c) 分块处理后
图9 45°铺层铺覆效果
2.4 -45°铺层的铺覆可行性分析
-45°铺层也出现了45°铺层一样的铺覆缺陷,只是位置不同。采取同样的剪口操作,如图10b所示,只有油底壳上侧有小片红色缺陷区域,可通过RTM模压工艺压实解决,整体的铺覆效果可以接受。
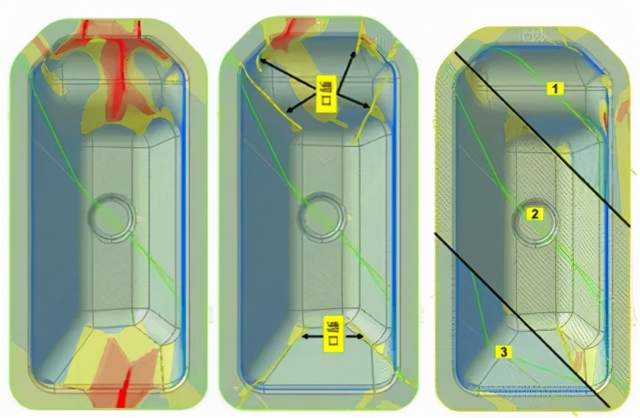
(a) 未处理 (b) 剪口处理后 (c) 分块处理后
图10 -45°铺层铺覆效果
2.5 剪口与分块方案分析及讨论
对油底壳模型的铺层设计采用了剪口和分块两种方案,为对后续实际工程应用中提供参考,现规定两个指标来选择最佳方案。
2.5.1 不合格率
不合格率即进行剪口或分块处理后,黄色区域与红色区域区域面积占总面积的比值,其中红色区域面积按实际面积的两倍计算,若铺层中不合格区域多,则在最终成型时会对碳纤维复合材料产品的力学性能造成影响。如图11所示,洋红色线包围区域为不合格区域,通过Catia软件对这些区域面积进行计算,并除以整层铺层的面积0.16 m2,便可算出两种方案下各角度的不合格率,如下表所示。
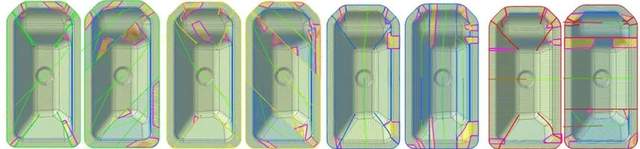
(a)0° (b)90° (c)45° (d)-45°
图11 剪口与分块方案不合格区域对比图
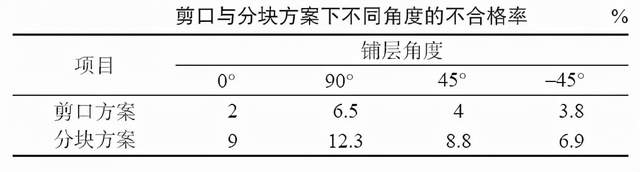
可以发现,剪口方案下,各角度铺层的不合格率都基本小于或等于分块方案的不合格率,这是因为剪口方案是对铺覆较差的区域进行处理,而分块处理要保证沿纤维方向的要求,存在局限性,会对铺覆效果好的地方造成损伤,导致铺层不合格率大于剪口方案。
2.5.2 完整度
完整度即油底壳周长与铺层展开后的总周长之比,碳纤维复合材料的传力性能是基于其自身的完整度实现的,对纤维破坏越小,一体化程度越高力学性能越高,因此对铺层完整度的比较,也是对其力学性能的重视。如图12所示,为两种方案不同角度的铺层展开图,通过Catia软件测量展开图的周长,再被油底壳的周长1243.8mm所除,便可得到如下表所示的完整度数值。
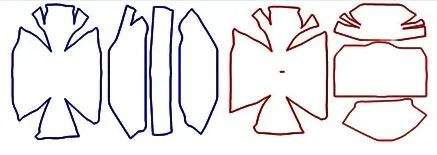
(a)0° (b) 90°
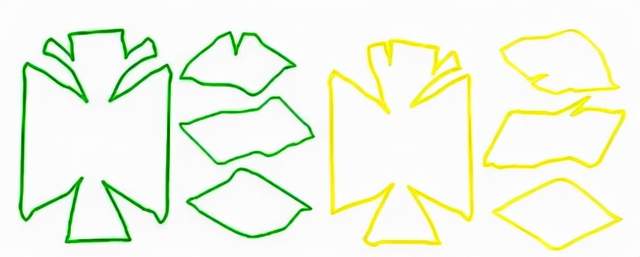
(c)45° (d)-45°
图12 剪口与分块方案铺层展开图
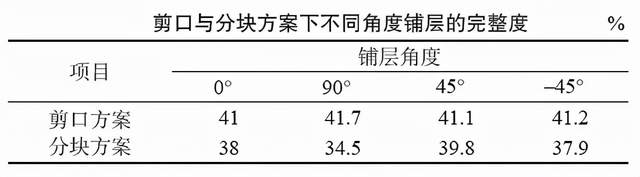
3 结论
通过对碳纤维复合材料油底壳的结构与工艺一体化设计,提出了针对汽车零部件的碳纤维复合材料化的设计方法和可行方案。首先对原金属结构进行简化使其符合碳纤维复合材料设计的要求,再通过等刚度替换原理初步确定结构厚度,基于Fibersim对铺覆可行性进行验证,最后得出如下结论:
•根据碳纤维复合材料零件的特点调整原金属油底壳的结构形状,并通过等刚度原理初步确定了碳纤维复合材料油底壳厚度为3mm,以每层碳纤维厚度为0.15mm设定碳纤维复合材料铺层设计为[455/-455/05/905];
•为保证铺覆可行性,依据复合材料层合板设计原则,将油底壳结构中所有小于5mm的圆角更新为5mm;
• 通过Fibersim软件验证了金属结构简化后的碳纤维复合材料油底壳结构可满足0°、90°和±45°铺层的铺覆要求,对比分析了剪口方案和分块方案的不合格率和完整度,最终确定剪口方案优于分块方案。
节选自秦晓宇,马其华,周琪,等.基于Fibersim的碳纤维复合材料油底壳设计[J].工程塑料应用
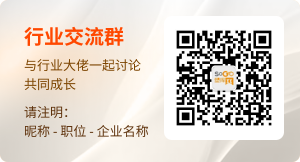