智能联网汽车的蓬勃发展,推动了电动制动系统对车辆安全与性能的重塑。齿轮传动式电动制动助力器和电子驻车制动系统,因其精准的控制与卓越的效率,市场需求迅速增长,预计到2026年,其年均复合增长率(CAGR)将分别高达26.4%和17.2%。恩骅力推出的Stanyl® PA46等先进热塑性塑料,助力电动制动系统高性能齿轮实现轻量化和高耐用性。
预计到2026年,年均复合增长率(CAGR)将高达
电动制动系统对执行器齿轮的性能提出了严苛的要求,尤其在自动紧急制动(AEB)等应用中,高扭矩会令部件和材料承受巨大应力。在高负载、高耐久性与紧凑型齿轮设计(执行器单元常见)并存的情况下,聚酰胺66(PA66)和聚甲醛(POM)等传统材料往往难以应对这些挑战。
在重载条件下,PA66和POM齿轮的轮齿易于发生开裂或变形,从而导致性能受损、可靠性下降。这些材料的热降解特性也进一步加剧了这一挑战:运行过程中产生的摩擦热会导致轮齿强度衰减甚至熔化,特别是在某些高负载蜗轮蜗杆设计(常见于电动制动执行器)所面临的高温工况下,情况尤为突出。
为提升PA66和POM材料的耐久性,所进行的增强改性尝试,其代价往往是齿轮尺寸偏大、厚度增加。此种体积过大的齿轮,难以满足电动制动执行器对紧凑型设计的要求,极大地限制了其在空间受限环境中的应用潜力。
这些局限性不仅增加了齿轮失效的风险,更带来了安全隐患,可能导致制动系统故障并引发灾难性后果。因此,面对下一代线控制动系统日益严苛且不断发展的要求,制造商亟需转向采用一系列先进材料,这些材料须具备高可靠性、更优越的紧凑设计以及更高的成本效益。
Stanyl® PA46 电动制动执行器应用的理想之选
恩骅力的Stanyl® PA46是一款高强度脂肪族聚酰胺,在电动制动执行器齿轮应用中表现出众。该材料的高结晶度以及卓越的耐热、抗疲劳和耐磨损性能,使其成为严苛汽车齿轮应用领域中,实现齿轮轻量化与高耐用性的理想选择。
Stanyl® PA46的核心优势:
这些特性使Stanyl® PA46成为实现紧凑型执行器设计的理想选择,助力制造商满足主机厂的严苛技术规格。
提升效率,节约成本
Stanyl® PA46不仅能提升齿轮性能,还具备以下额外优势:
采用Stanyl® PA46,将助力齿轮供应商在激烈的市场竞争中脱颖而出,实现高品质部件的高效交付。
凭借在汽车行业逾20年的专业积淀,恩骅力已成为全球顶尖主机厂、一级供应商及齿轮制造商的优选合作伙伴。每年全球有近1亿件采用Stanyl® PA46材料制造的齿轮,装配在4000万个执行器中,在电动制动、底盘系统、发动机、冷却及动力总成等关键系统上发挥着重要作用。
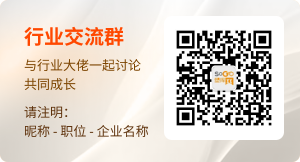