填料会打破机筒与螺杆之间的摩擦拖曳平衡,妨碍材料向机筒下游移动——除非在挤出过程中采取一些补偿措施。
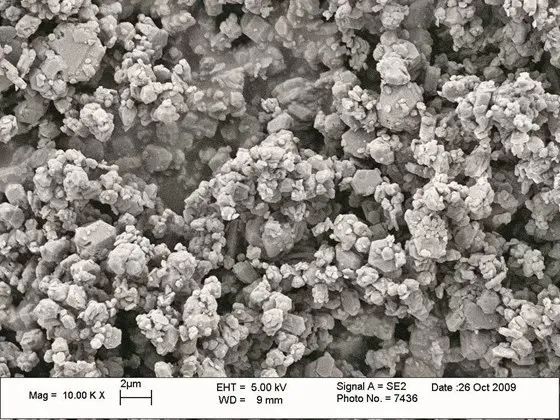
加工者挤出填充聚合物有年矣。一般而言,填料百分比通常小于30%的重量比,或者10-15%的体积比,因为填料的比重是聚合物的3-10倍。
近来,一些新开发的共混物甚至含有填料达85%重量比,这导致填料在体积上超过了聚合物。这些混合物在传统螺杆设计上通常不能正常挤出。
想要解决这个问题,需记住固体喂料的基本原理:
要想聚合物粒子向前流动,材料相对于机筒比相对于螺杆必须具有较小的拖曳。在喂料段,螺杆表面积通常比机筒面积大很多;该比例称之为径厚比。为了抵消径厚比的影响,驱动粒子向前所需要的拖曳力一般通过加热机筒或者通过改变表面粗糙度而产生出来,以此增大拖曳力。
输送摩擦
但是,许多典型填料具有棱角或形状不规则,具有相当大的摩擦力。因此,当径厚比在1.25:1到1.35:1时,我们难于增加机筒内壁的摩擦拖曳来抵消对螺杆表面的拖曳。对机筒增加热量可能使事情变得更糟,因为其实施方法是熔融机筒壁附近的聚合物,相对于螺杆拖曳减少了机筒拖曳。
在某些情况下,可能需要反转标准的固体喂料工艺,以减少相对于螺杆表面的摩擦拖曳,其实施方法是工艺性质的,例如对聚合物进行预热,或者使用加热螺杆,涂层或加工助剂。
压缩比
压缩或者压缩比,在传统聚合物螺杆中是必要的,因为聚合物粒子一般具有较低的喂料效率以及需要解决熔体形成和输运的影响,由此可以允许熔体比固体流动更快。反过来,某些填料粒子的几何形状改进了固体喂料效率,因为这些固体颗粒不互相滑移。这就不需要那么高的压缩比而达到所要求的喂料速率。
由于填料是不熔融的,它们不流动,所以,混合物的流动性质就是固体粒子性质与标准熔体流动的一种综合性质。结果,随着螺槽体积沿着长度方向减少,具有用于纯聚合物的压缩段的螺杆,只是以填料填满螺槽,因为缺乏填料的流动。
此外,随着压缩的进行,在填充共混物中的少量聚合物可能会被挤压出来,结果只剩下被紧密压缩的填料。由于螺杆基本上是一个螺旋的楔形结构,即使没有压缩,填料也能被压紧,以至于可以弄停马达或者甚至弄断螺杆。因此,某些零压缩比或者负压缩比的螺杆发现也能有效工作。
温度控制
一旦喂料被建立,熔融在某些方法下就变得更容易,而在另一些情况下则变得困难。没有了标准的螺槽压缩,传统的熔融机理就牺牲很多,熔融就更多地是基于传导加热而不是剪切加热。螺杆设计,基本上通过旋转或破碎位于螺槽中的聚合物而暴露更多的表面面积,它常常比屏障型设计或高剪切混合器更有效。
由于许多填料比聚合物具有更低的比热,所以,升高一磅混合物到加工温度所需要的能量就大为减少。此外,许多填料比聚合物具有更高的导热率,有助于导热和熔融。
在加工高填充聚合物的螺杆设计上,有少量的通用规则可以遵循。
1.熔融完成后,剪切热往往成为问题,因为高填充填料在许多情况下极大地增加了粘度并减少剪切变稀,所以,熔融完成后的段长应该缩短。
2.上下游变化要另行讨论。由于架桥/压紧,填料影响进入螺杆的速度,并通过高粘聚合物的加工引起更多的压力降低。
3.螺杆中的压力建立也是具有较少预测性的,更多的是变动的,因为填料常引起熔体的不连续性以及填料对机筒内壁的冲刷。
不幸的是,在加工高填充聚合物的螺杆设计上,只有少量的通用规则可以遵循。所以,更多的是取决于填料粒子的特征、混合物组分的比例、熔融聚合物的粘度、混合物的熔融速率以及螺杆和机筒的温度。
同样需要注意的是,高填充料的生产需要螺杆、基础设备、喂料设备等上下游设备及操作步骤上进行变化,这需要供应商的集体努力。
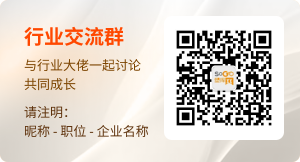