开裂,包括制件表面丝状裂纹、微裂、顶白、开裂及因制件粘模、流道粘模而造成的创伤,按开裂的时间分为脱模开裂和应用开裂。
本文通过对一则客户委托失效分析案例进行复盘,为大家进行制件开裂失效分析提供切实有效的分析思路及分析方法。
一、开裂失效情况描述
PC/ABS手机外壳,产品侧边在化学品测试时开裂。
二、制件开裂原因调查
- 产品设计检查
该产品为嵌件成型,因金属嵌件限制了塑胶的收缩,因此会产生了残余应力。
以不放金属嵌件的产品进行化学品测试,没有出现开裂问题,因此证实嵌件成型产生的内应力是化学品开裂的根本原因。
开裂位置的塑胶较少(宽度小),属于塑胶强度较弱的位置。
- 模具设计检查
开裂发生在充填末端,远离浇口的收缩率更大,收缩应力也会更大。同时开裂位置也是结合线所在,是产品强度较弱的位置。
三、可能原因分析以及改善措施
- 1、优化产品设计
上述设计有利于降低侧边因金属嵌件与塑胶收缩差异产生的收缩应力,以及将结合线移到更高强度的位置。
- 2、优化成型工艺
根据DOE实验,增加保压压力和保压时间,开裂比例有改善,但不能完全避免开裂。
- 3、优化材料方案
材料DOE结果如下:
PC EXL1414 没有改善
C1000HF 有改善
PC 10%GF 未发现开裂
结论:玻纤增强和高流动规格有助于改善开裂问题。
- 4、二次加工工艺
产品有喷涂,稀释剂对产品有攻击。降低稀释剂的强度有助于改善开裂。
四、潜在改善对策与结果
1、优化工艺条件来降低收缩应力
2、改进油漆配方,减少对产品的攻击
3、更换玻纤增强材料
4、模具浇口变更,改变结合线位置
结果:保压压力由1500kgf/cm² 增加到2200kgf/cm² ,以及改进油漆配方后通过了测试。
欢迎交流
好的经验总能为我们带来新的启发,学习并付诸于实践,可以不断提高我们分析问题、解决问题的能力,成为一名可以自主解决各种注塑缺陷的高手。
针对今天的案例,大家如果有更好的想法,欢迎加入我们的行业交流群,参与讨论。
课程推荐
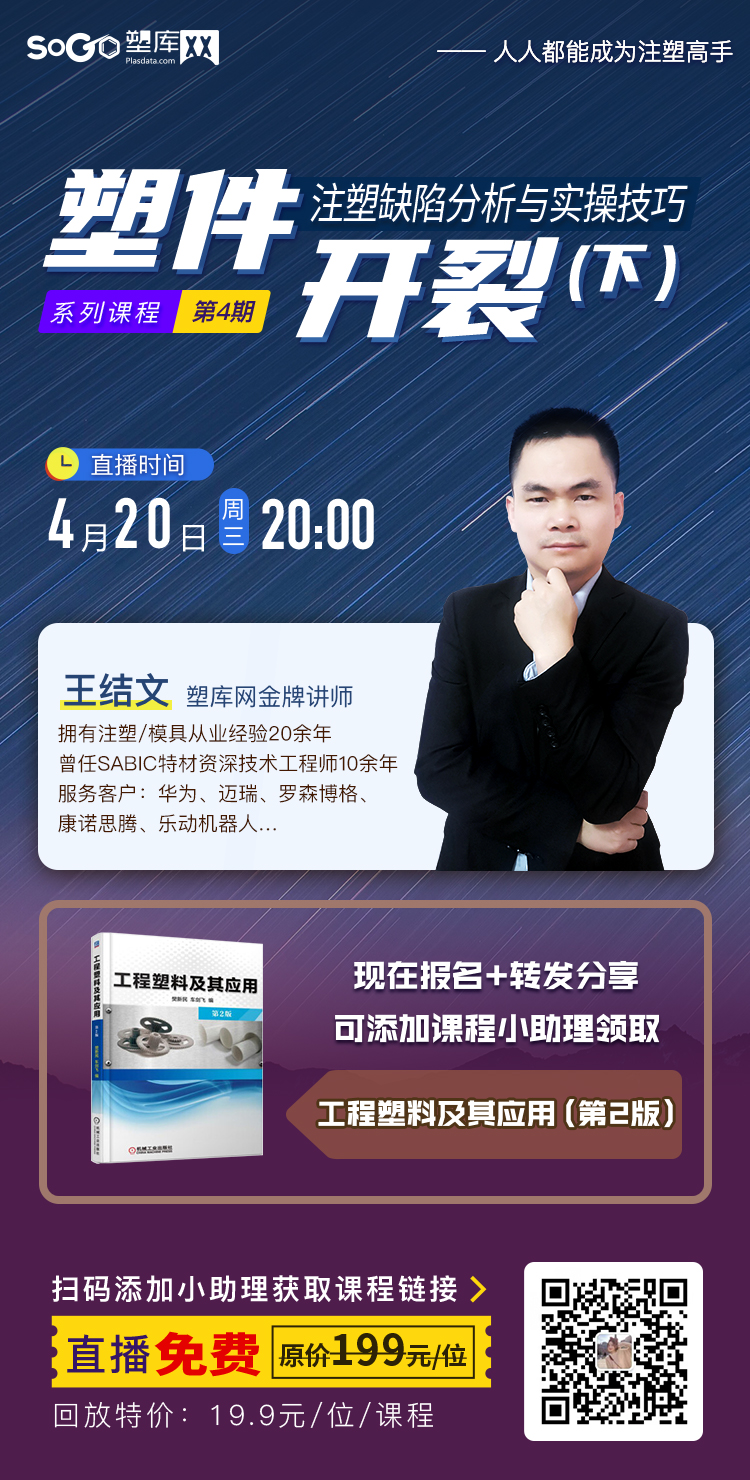
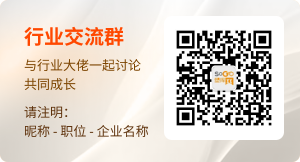