摘要:塑料零件在受到挤压摩擦时,容易发生粘滑现象,从而产生异响,目前汽车行业普遍采用的涂抹润滑油、消音水、粘贴无纺布类毛毡等措施增加了产品的生产周期与成本。针对上述情况,并基于吉利汽车标准,通过添加热塑性聚酯弹性体(TPEE)与聚碳酸酯/丙烯腈-丁二烯-苯乙烯塑料(PC/ABS)共混改性,研发出了一款具有优异降噪功能的PC/ABS材料,对比了降噪PC/ABS与普通PC/ABS的常规性能和降噪性能。
结果表明,与普通PC/ABS相比,降噪PC/ABS的力学性能略有降低但保持了良好的耐刮擦性能、耐化学药品性以及耐光老化性能,而且具有更低的响度、更小的振动加速度以及更低的异响风险系数值,最终成功应用在多个车型的仪表板部件上,实现国产降噪材料的成功量产。
关键词:异响;聚碳酸酯/丙烯腈-丁二烯-苯乙烯塑料;降噪;汽车仪表板
聚碳酸酯(PC)/丙烯腈-丁二烯-苯乙烯塑料(ABS)合金具有易加工、韧性好、耐应力开裂、耐候性好等优点,广泛应用于汽车及其它行业[1–3]。但是,使用PC/ABS材料的零件在发动机行驶振动或受到外力挤压作用时,容易产生“吱吱”的异响声。这种异响声可能来自于塑料制件之间的摩擦,也可能来自塑料件与皮革件、电镀件等之间的摩擦[4]。
零件受到外力时,发生了粘滑现象,塑料件由相粘的静摩擦状态转变为滑动接触,并且此过程有能量释放,粘滑循环发生导致材料振动产生异响[5–6]。
阻尼性能是指固体机械振动能转变为热能的能力,主要用于振动和噪声控制[7–9]。材料的阻尼性能越好,说明摩擦功转化为内能越多,材料异响越小。高分子材料的阻尼作用机理与其自身的动态松弛性质有关。
当高分子材料受到交变应力的作用时,由于链段运动时受到内摩擦作用,形变通常落后于应力的变化,产生一个相位差滞后角,这种现象称为滞后现象[10–12]。由阻尼产生的机理可知,能够增大分子内摩擦的因素便可提高材料的阻尼性能。
吉利汽车通过易产生异响的零部件研究发现,容易产生异响的主要原因见表1。
现阶段,主机厂主要是通过在接触部位增加毛毡阻隔、涂覆润滑油、使用橡胶衬垫等措施解决制件的摩擦异响[13–17],但是这不仅增加了人工成本,而且延长了产品的生产周期。
因此,降噪改性成为了塑料改性厂商关注的焦点[17]。余朦山等[18]通过引入马来酸酐接枝的聚氨酯树脂对ABS进行共混改性获得了高阻尼降噪材料;J.Rojsatean等[19]发现乙撑双硬脂酰胺(EBS)和乙烯–辛烯共聚物(POE)的加入也能够有效地改善ABS的粘滑倾向。卢焕青[20]发现热塑性聚酯弹性体(TPEE)兼具橡胶优良的弹性和热塑性塑料的易加工性及良好的声阻性能。
但是,目前国内还没有能实现稳定量产的TPEE改性PC/ABS降噪材料。基于此,吉利汽车与锦湖日丽合作从改善材料阻尼性能和摩擦系数角度出发,通过材料研发与零件验证,最终将降噪PC/ABS合金成功应用于吉利多款车型的仪表板上。
实验部分
1.1 主要原料
PC:7025J,日本三菱化学公司;
ABS:8434,中国石化高桥石化公司;
抗氧剂1010、抗氧剂168:瑞士汽巴(Ciba)精细化工有限公司;
季戊四醇硬脂酸酯(PETS):意大利FACI公司;
TPEE:TX506,中国石化仪征化纤股份有限公司。
1.2 主要仪器与设备
双螺杆挤出机:CET35型,长径比为44∶1,科倍隆(南京)机械有限公司;
塑料注射成型机:JM138–AI–SVP/2型,震雄机械(深圳)有限公司;
密度仪:GR–200型,日本A&D公司;
电子万能拉伸试验机:Z010型,德国ZwickRoell集团;
摆锤冲击试验机:HIT25P型,德国ZwickRoell集团;
热变形维卡试验机:IC6+型,德国Coesfeld公司;
刮擦仪:ERICHSEN430P型,德国仪力信公司;
氙灯老化试验机:Ci3000型,美国Atlas有限公司。
1.3 试样制备
降噪PC/ABS:将PC,ABS,TPEE及抗氧剂和润滑剂PETS按照质量比65/27/8/0.5/0.5进行混合(抗氧剂1010与168质量比为1/1,下同;小试实验中,当TPEE用量低于8份时其对材料的降噪效果不大,而当TPEE用量高于8份时会影响相容性从而影响材料冲击性能),然后在双螺杆挤出机上进行熔融挤出造粒。挤出机的温度为200~250℃,螺杆转速为350r/min,相对真空度为–0.09MPa;将所制得材料在100℃下干燥4h,然后注塑成样板(140mm×90mm×3mm),其中注塑温度为250℃,注塑压力为80MPa,成型周期为50s。
普通PC/ABS:将PC,ABS,抗氧剂和润滑剂按照质量比65/35/0.5/0.5混合,其余步骤同上。
1.4 性能测试
(1)常规性能测试。
密度按GB/T1033.1–2008测试;
拉伸强度按GB/T1040.1–2018测试,拉伸速率为50mm/min;
弯曲强度与弯曲弹性模量按GB/T9341–2018测试,弯曲速率为2mm/min;
悬臂梁缺口冲击强度按GB/T1843–2008测试,摆锤能量为4J;
维卡软化温度(B50法)按GB/T1633–2000测试;
耐化学药品性按Q/JLYJ711028E–2019测试;
耐刮擦性能按Q/JLYJ7110536C–2019测试;
耐光老化性能按Q/JLYJ7110279B–2014测试。
(2)摩擦异响试验。
摩擦异响试验设备为锦湖日丽自行搭建,具体实验条件及参数见文献[4],设计的工装结构如图1所示[4]。压头和样板之间摩擦时易产生典型的粘滑现象从而产生振动和噪音。将振动传感器粘贴在摩擦压头上采集摩擦过程中产生的振动参数,即振动加速度;声音传感器距待测样板5cm采集声音参数,即人耳响度。
(3)异响测试。
根据标准VDA230–206–2005测试异响的风险系数(RPN)。待测样品与摩擦副的接触面积为1250mm2,滑动距离固定为50mm,滑动速度为1mm/s和4mm/s,负载为10N和40N。测试前将样品在温度(23±2)℃,相对湿度(50±5)%环境中调节24h以上。
(4)零部件试验。
用普通PC/ABS和降噪PC/ABS分别注塑成如表2中的部件进行异响对比验证,由7人进行评级取众数。其中评级为1级代表无异响,2级代表轻微异响,3级代表异响较重,4级代表异响严重。
2.1 降噪PC/ABS与普通PC/ABS的常规性能对比
表3列出降噪PC/ABS与普通PC/ABS常规性能的对比。由表3可以看出,降噪改性后的PC/ABS在刚性方面(拉伸强度、弯曲强度和弯曲弹性模量)略有下降,这是因为TPEE弹性体分子链的柔性链段可以有效增大分子内摩擦,从而降低材料刚性、增强材料的阻尼性能。缺口冲击强度的小幅减小可能归因于TPEE的加入一定程度降低了PC与ABS之间的相容性。另外,改性后的PC/ABS在耐化学药品性、耐刮擦性能、耐光老化性能等方面与普通PC/ABS相媲美,均能达到汽车内饰的行业标准。总体来看,两种材料的常规性能差别较小。
2.2 人耳响度结果分析
响度又称音量,单位为宋,它是人对声音大小的主观感觉量。其大小决定于声音接收处的波幅,表示人耳对声音的直观感受。图2是不同PC/ABS材料的响度随摩擦时间的变化曲线,可以看出,降噪改性的PC/ABS在摩擦过程中产生的响度(30宋)远低于普通PC/ABS(62宋),这体现出了其优异的降噪效果。
2.3 振动加速度分析
声音伴随着振动,频率越高,振动越剧烈,意味着制件接触时产生异响的风险越大。图3是不同PC/ABS材料的振动加速度随着摩擦时间的变化曲线,可以看出降噪PC/ABS在摩擦过程中的加速度远低于常规PC/ABS,进一步验证了改性PC/ABS优异的降噪性能。
2.4 异响RPN结果分析
RPN是事件发生的频率、严重程度和检测等级三者的乘积,被称为风险系数或风险顺序数,其数值越大说明潜在问题越严重。一般认为,当RPN=1~3,材料发生异响的风险较小;当RPN=4~5,材料存在中等异响的风险;当RPN=6~10,材料存在较高的异响风险。不同PC/ABS材料的异响RPN数据见表4。由表4可以看出,无论测试压力或者滑动速度如何,降噪改性PC/ABS都展示出极低的异响RPN值,该结果说明材料发生异响的风险较低。
2.5 零件试验结果
通过表2的零部件异响验证,得到普通PC/ABS和降噪PC/ABS的异响结果,见表5。由表5可以看出,降噪改性的PC/ABS在太阳暴晒下经历按压或者开空调操作均无任何异响。在崎岖道路与减速带验证环节,与普通PC/ABS相比,改性PC/ABS也表现出了更加优异的降噪效果。
塑料零件在受到外力挤压时,容易发生粘滑现象,从而产生异响。通过共混改性方式研发出了一款降噪性能优异的PC/ABS合金材料。与传统的PC/ABS合金相比,它的拉伸强度、弯曲强度、弯曲弹性模量以及缺口冲击强度略有降低,但是都能满足仪表板部件的标准要求。
值得关注的是,TPEE的加入使得PC/ABS合金具有更低的响度、更小的振动加速度以及更低的异响RPN值,从而具有优异的降噪效果,最终应用在多个车型的仪表板部件上,实现国产降噪材料的成功量产。
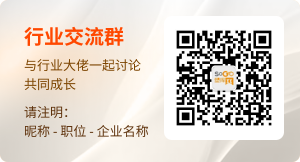