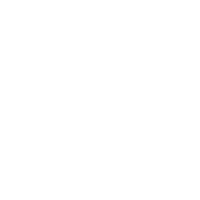
DuPont™ Liveo™ Pharma TPE Tubing
Sterilizable, weldable TPE tubing for biopharmaceutical processing
With the launch of new Liveo™ Pharma TPE Tubing, DuPont is now offering a thermoplastic elastomer (TPE) option for fluid transport and single-use bioprocessing applications and is facilitating adoption and compatibility with leading competitive TPE tubing offerings.This new product range complements our silicone-based Liveo™ Pharma Tubing and Overmolded Assemblies product lines and is produced under the same high quality principles as the products our customers already know and trust.
Key features and benefits
- Improved heat-welding, both to
itself and to competitive offerings
- High tensile strength and burst
resistance before and after welding
- Low extractables
- Good chemical resistance
- Minimal spallation after 24 hours
of pumping
- Good clarity; stable clarity after
sterilization
- Manufactured in ISO Class 7
cleanroom
Comprehensive data package to accelerate qualification and validation under the form of a qualification guideApplications
- Fluid, media and solvent transport in biopharmaceutical processes and biotechnology
- Single-use assemblies
- Peristaltic pump applications
- Aseptic connection and disconnection without connectors(e.g., sampling)
- Applications where compatibility with industry benchmark TPE tubing is needed
Typical physical properties of Liveo™ Pharma TPE Tubing
Properties are based on Liveo™ Pharma TPE Tubing with an inner diameter (I.D.) of 3/8" (9.5 mm) and an outer diameter (O.D.) of 5/8" (15.9 mm). Specification writers: These values are not intended for use in preparing specifications. Please contact
DuPont prior to writing specifications on this product.
Purity data for Liveo™ Pharma TPE Tubing
- USP <85> (Endotoxins)
- USP <665> (Extractables and Leachables) with autoclave or gamma radiation sterilization methods
- USP <788> (Particulates)
- ISO 11737-1 (Bioburdens)
Regulatory data for Liveo™ Pharma TPE Tubing
- ISO 10993 Biocompatibility tests (5: Cytotoxicity, 6: Muscle Implantation,11: Acute Systemic Toxicity, 23: Intracutaneous Irritation)
- USP Class VI (Intracutaneous Reactivity, Acute Systemic Injection,Intramuscular Implant)
- Pyrogenicity (USP <151>)
- Elemental Impurities
Sterilization methods
DuPont™ Liveo™ Pharma TPE Tubing is sterilizable using the following methods:
- Steam (1 autoclave cycle of 30 minutesat 121°C)
- Gamma radiation (up to 50 kGy)
Performance data for DuPont™ Liveo™ Pharma TPE Tubing
Comprehensive studies were conducted on material in common sizes and using different sterilization methods, including steam and gamma radiation.The following is a review of analyses comparing Liveo™ Pharma TPE Tubing to industry benchmark tubing. Further testing data is available; please contact DuPont for more details depending on your application needs.
Benchmark analysis: Summary of typical performance
Test samples steam-sterilized (autoclaved 1 cycle of 30 minutes at 121°C);0 = lowest performance; 5 = highest performance.
Results
Liveo™ Pharma TPE Tubing showed better tensile strength after welding than the benchmark tubing.Testing also revealed better welding strength and burst pressure resistance by Liveo™ Pharma TPE Tubing versus the benchmark tubing. Excellent welding strength and burst pressure resistance enable Liveo™ Pharma TPE Tubing to improve the safety margin during fluid transfer applications.
Testing protocol
- Weldability was assessed by sterilization of the samples prior to running specific testing to measure the ability of the welded section to withstand mechanical stress before failure was observed.
- The specimens were welded using the specific Biowelder® TC preprogrammed setting.
- Tensile strength of the welded section was determined from the average maximum tensile strength as measured on dumbbells cut out from the tubing using ASTM D412 Die C.
- Liveo™ Pharma TPE Tubing welded extremely well to itself and to the benchmark tubing using aseptic tubing welders/ standard recipes.
- Burst pressure resistance properties were determined according to ASTM D380 in a burst chamber apparatus by flowing water through the tubing and increasing the water pressure until ballooning and burst eventually were observed.